LifeCycle360
Your Single-Source Support Services
Lifecycle360 offers seven support services designed to help you and your team streamline and optimize the full lifecycle of your facility, from pre-engineering to long-term maintenance needs. Each Lifecycle360 support service is optimal at a different stage of a plant’s lifecycle and can be engaged à la carte or in combination with the final equipment, parts or technology package.
Every opportunity is unique, and our talented support specialists have the experience that enables them to develop the ideal solutions that fit your needs. We are your single source for the planning, coordination and support that will help secure the success of your investment and help you gain the edge on your competition.
LifeCycle360
Support Services:
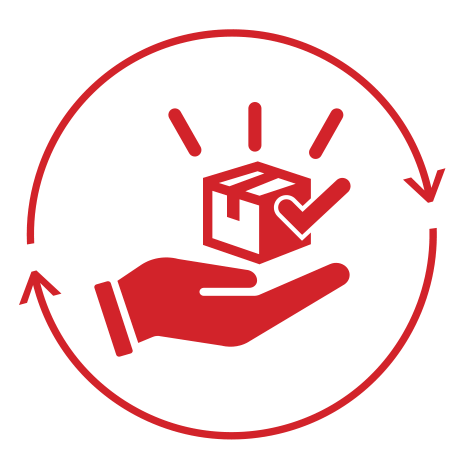
Innovation Services
Confidential Development, Testing and Commercialization for Your Next Innovation
For customers seeking a state-of-the-art piloting and testing facility to help them meet goals for product development, process improvements, product and process commercialization, speed to market, employee performance and more.
Piloting & Testing Services
CPM|Crown’s Global Innovation Center has best-in-class equipment and resources for testing and piloting in:
- Preparation
- Extraction
- Specialty extraction (including Hemp CBD Oil)
- Desolventizing
- Drying
- Deodorizing
- Refining
- Fat splitting
- Renewable diesel/SAF pretreatment
Benefits
- Explore new products, new feedstocks and improve go/no-go decisions
- Gather data on test samples created at the GIC that enable you to move from benchtop to commercialization with confidence
- Bring products to market faster
- Engineer unique, better processes
- Troubleshoot existing equipment
- Test and integrate operational advancements
- Increase accuracy of cost estimates
- Gain better control over your processes
- Single-source testing and piloting facility – we have capabilities for every step of the process
- Collect and act on insights from PLC & Data Historian
Contact Us »
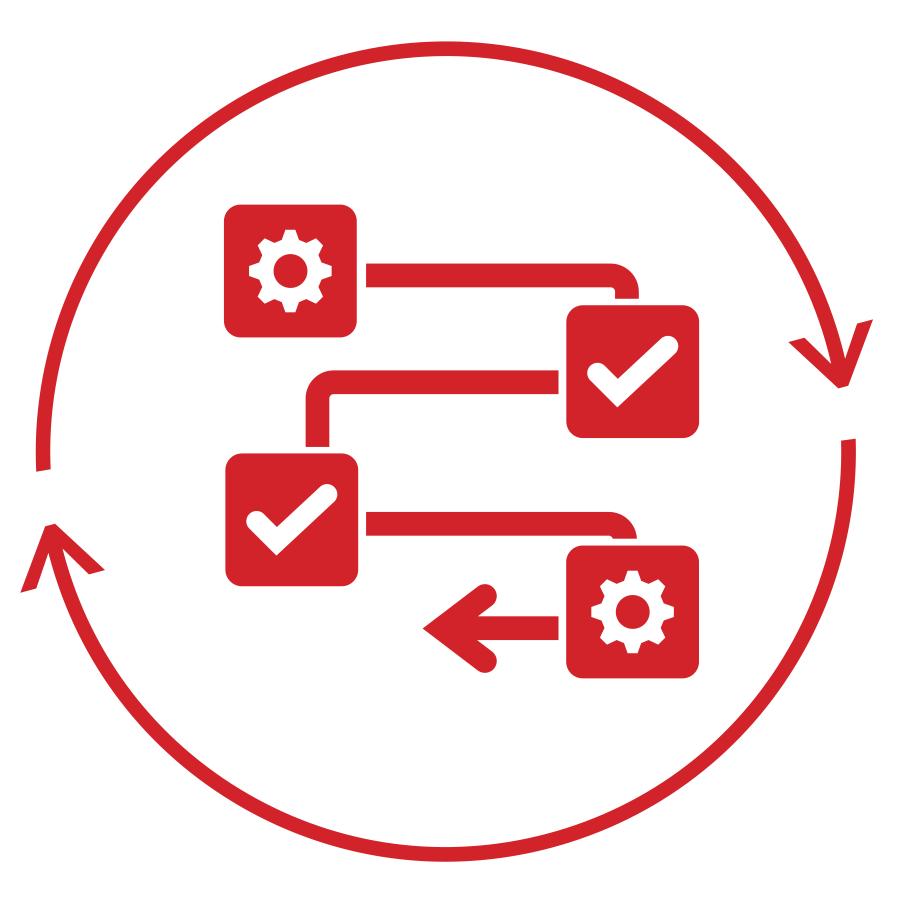
Pre-Engineering Services
Technology Deep Dive for Investment Confidence
Conceptual Engineering Services
- Block flow diagrams
- High-level utility requirements
- Facility footprint
- Flowsheet with key pieces of equipment
- Proposal for process-related equipment
Pre-Engineering Services
- Preliminary Process Flow Diagrams (PFDs) with mass and energy balance
- Preliminary Piping and Instrumentation Diagram (P&ID)
- Preliminary motor and instrument lists
- Preliminary equipment list
- Firm proposal for process-related equipment
Benefits
Conceptual Engineering:
- Engage with commercial subject matter experts (SMEs) to better understand project scope and get budget quotes
- Multiple process configuration options evaluated
- Enables +/- 50% investment confidence
Pre-Engineering:
- Engage with operational SMEs to better understand scope, get budget quotes and get better-quality deliverables
- Enables +/- 20% investment confidence
Contact Us »
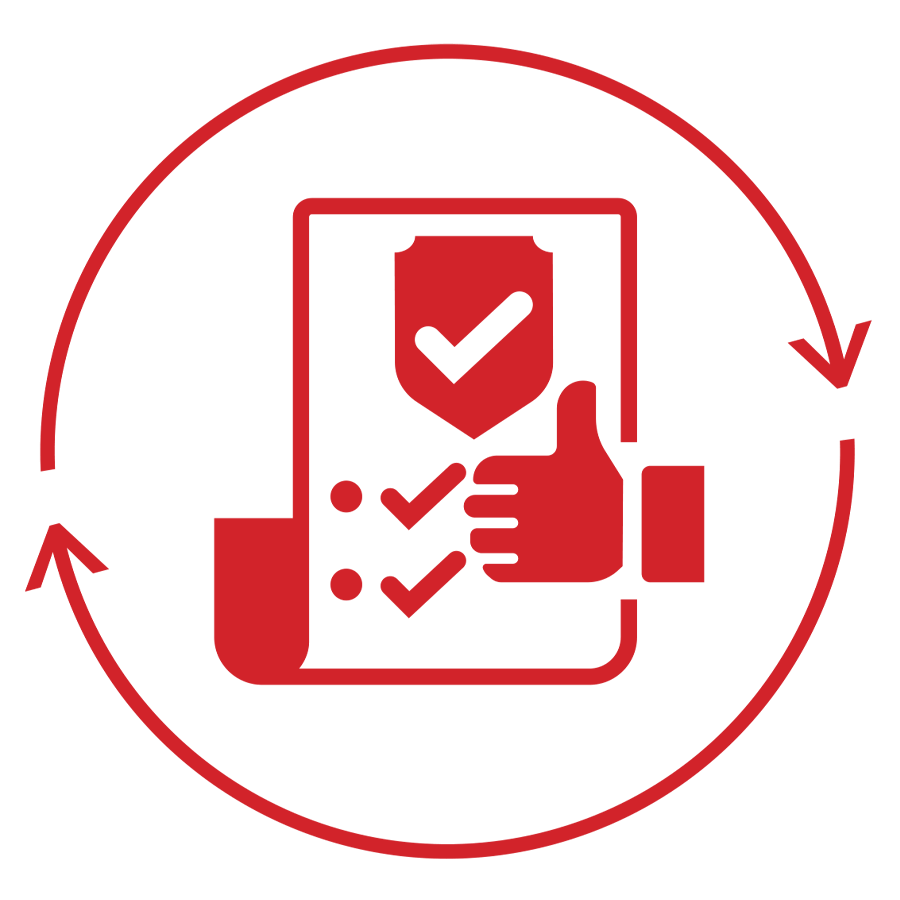
Construction Support Services
Less Construction Hassle. Reach Profitability Sooner.
For clients executing projects involving our technology who want to achieve faster startup timelines, low-hassle startups, reduced re-work and change-order costs, and faster business returns.
Consultation and Support Services
- Assessments
- Installation Planning
- EPC Bid Package Planning
- EPC Training
- Equipment Installation Support
- Mechanical Check-outs
- Parts Organization
- Process Commissioning and Startup
- Process Hazard Analysis Technical Support
Benefits
- Maximize investment
- Better awareness and coordination throughout the process
- Reduce emergencies and construction change orders
- Save frustration with trouble-free startups
- Avoid miscommunication and confusion
- Facilitates continuity with aftermarket services
Contact Us »

Automation Services
Secure Automation Backed by Unmatched Experience
For clients seeking to upgrade their automation to achieve production, safety, environmental, and financial goals.
Services
- Assessments and optimized recommendations
- Controls and instrumentation upgrades
- Safety and hazard analysis
- Programming and HMI designs
- Integrated Industrial Internet of Things
- Process commissioning and startup support
- Upgrade services
Benefits
- Typical payback in less than 2 years
- Make data-driven, real-time decisions
- Peace of mind knowing that your operation is running at max efficiency
- Simplification – save time and reduce hassles of coordinating services
- Coordinated out-of-the-box solutions minimize ramp-up time, resulting in greater time savings
- Single solutions provider leaves no gaps in strategic planning and execution
Contact Us »
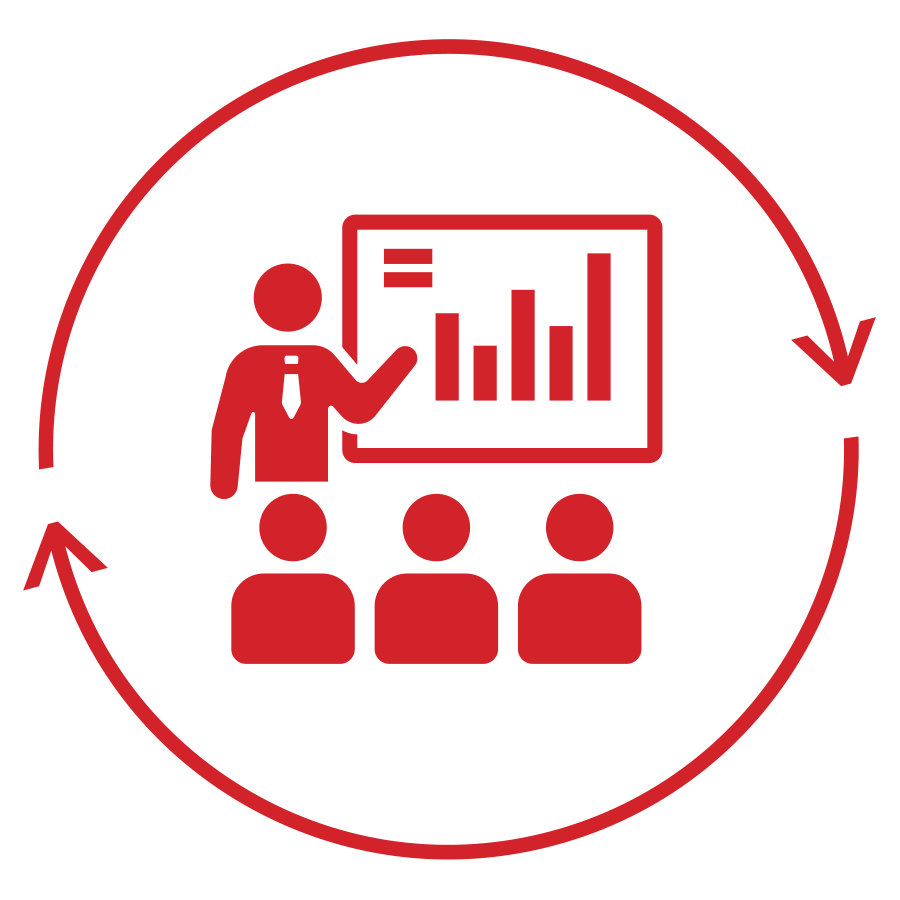
Training Services
Specialized Team Training for Safe, Smooth, Efficient Operations
Services
- Training needs assessment
- On-site professional training
- Classroom
- Hands-on field training
- CPM|Crown Global Innovation Center and Training Facility
- Training modules include:
- All CPM | Crown processes and technology
- Plant theory, operation, safety, maintenance and automation
- Training modules selected based on customer needs and audience level (basic, advanced, custom)
- Access to specialized training from over 200 subject matter experts
Benefits
- High-impact training from dedicated team of professional training specialists
- Employee training increases plant safety and promotes efficient plant operation and consistent product quality
- Higher employee confidence, job satisfaction and retention
- Employees understand the fundamentals underlying plant and equipment operation, improving real-time decision making
- Dynamic, experiential learning on real operating equipment
Contact Us »
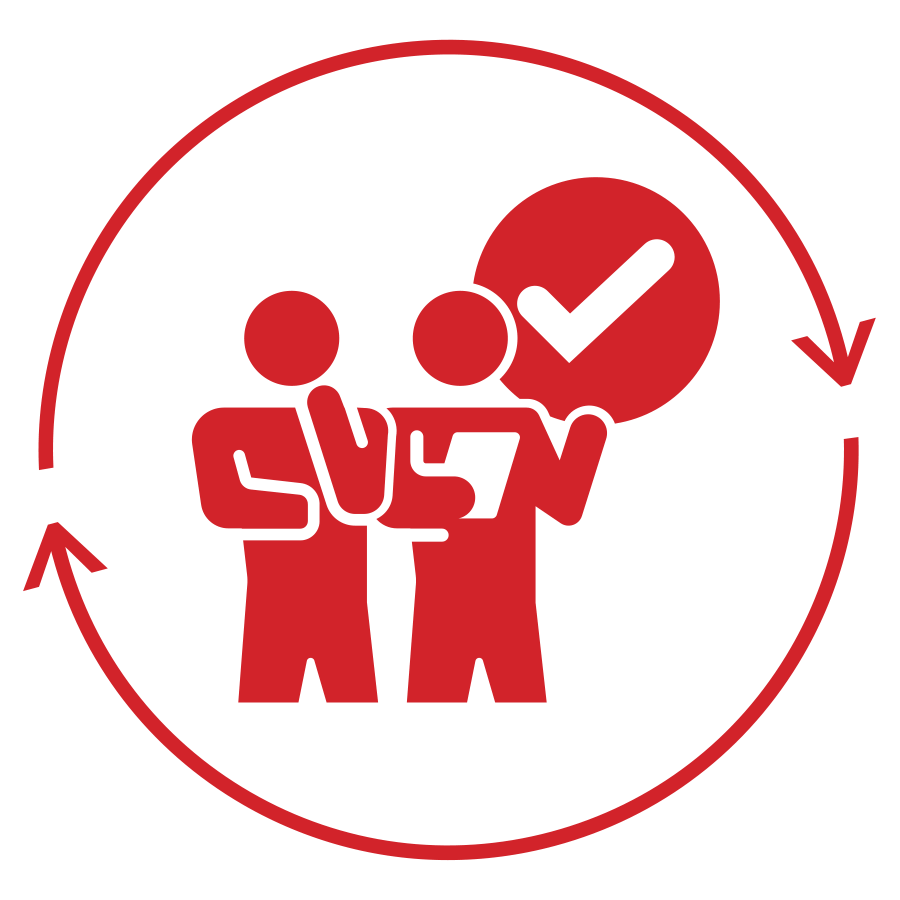
Maintenance Support Services
Maximize Uptime, Reduce Costs with Comprehensive Maintenance
Consultation and Support
- Site assessments
- Preventative maintenance plan development
- Shutdown pre-planning and technical support
- Steam purge support to minimize prep time for annual hot work
- Coordination with CPM for retrofits, service enhancements and expansions
- Plant and equipment inspections (mechanical integrity, process, parts wear, inventory evaluation)
- Parts organization and installation support
- Asset management guidance
- Critical spare identification
- Periodic maintenance, process review and follow-up
Benefits
- Maximize facility uptime
- Proactive, predictive planning minimizes surprises and costs
- Minimize unplanned shutdowns
- Get the correct parts when you need them
- Maximize life of equipment and parts
- Minimize replacement cost through long-term planning – no more expediting
- Better parts inventory management
- Stay current with the newest, improved parts and equipment
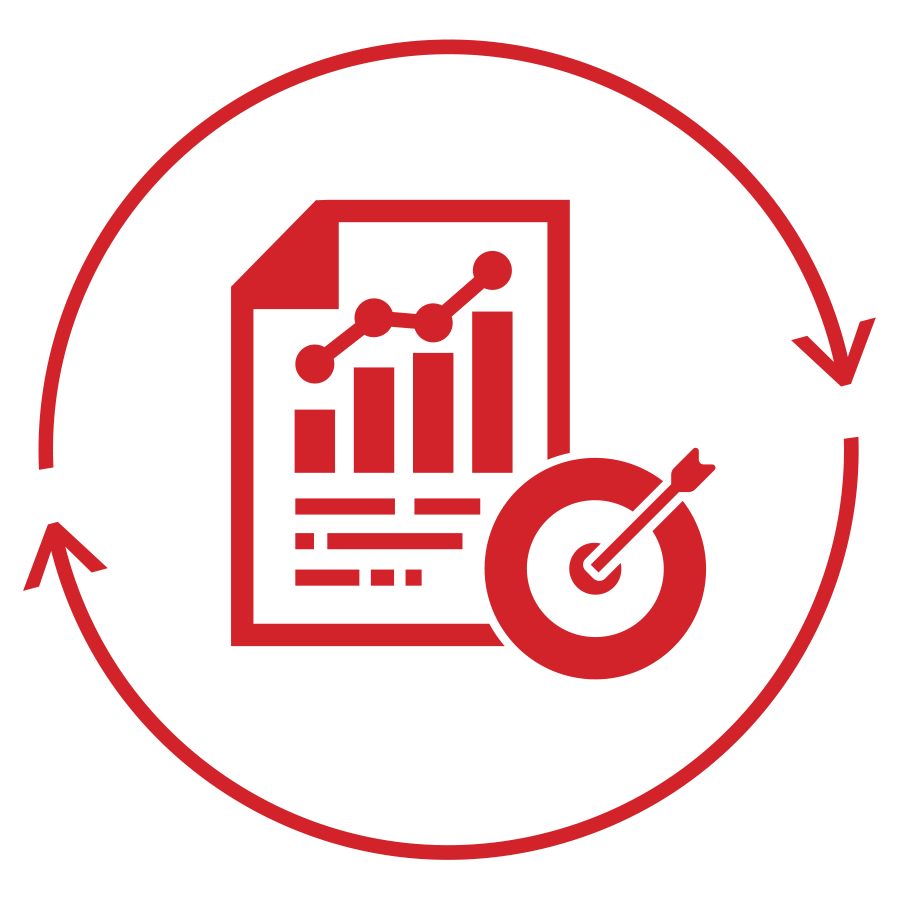
Optimizing Services
Unlock Your Plant’s Full Potential
Services
- Assessments
- Analysis
- Modeling
- Debottlenecking
- Delivering both the engineered solution and the recommended equipment/technology
Benefits
- Improve yields, capacity, and energy, water and waste usage
- Achieve environmental goals and overcome environmental challenges (reduce utilities consumption, decrease water usage, minimize wastewater)
- Holistic overview of whole facility (interactions between upstream and downstream equipment)
- Identify and resolve equipment/process inefficiencies
- Payback typically < 2 years
Achieve Your Best Results With Our Trusted Team of Support Specialists
When you combine CPM|Crown’s robust equipment and technology with our Lifecycle360 Support Services, you will have peace of mind knowing that an experienced, dedicated and trusted partner has your back at every stage of your plant’s lifecycle.
LifeCycle360
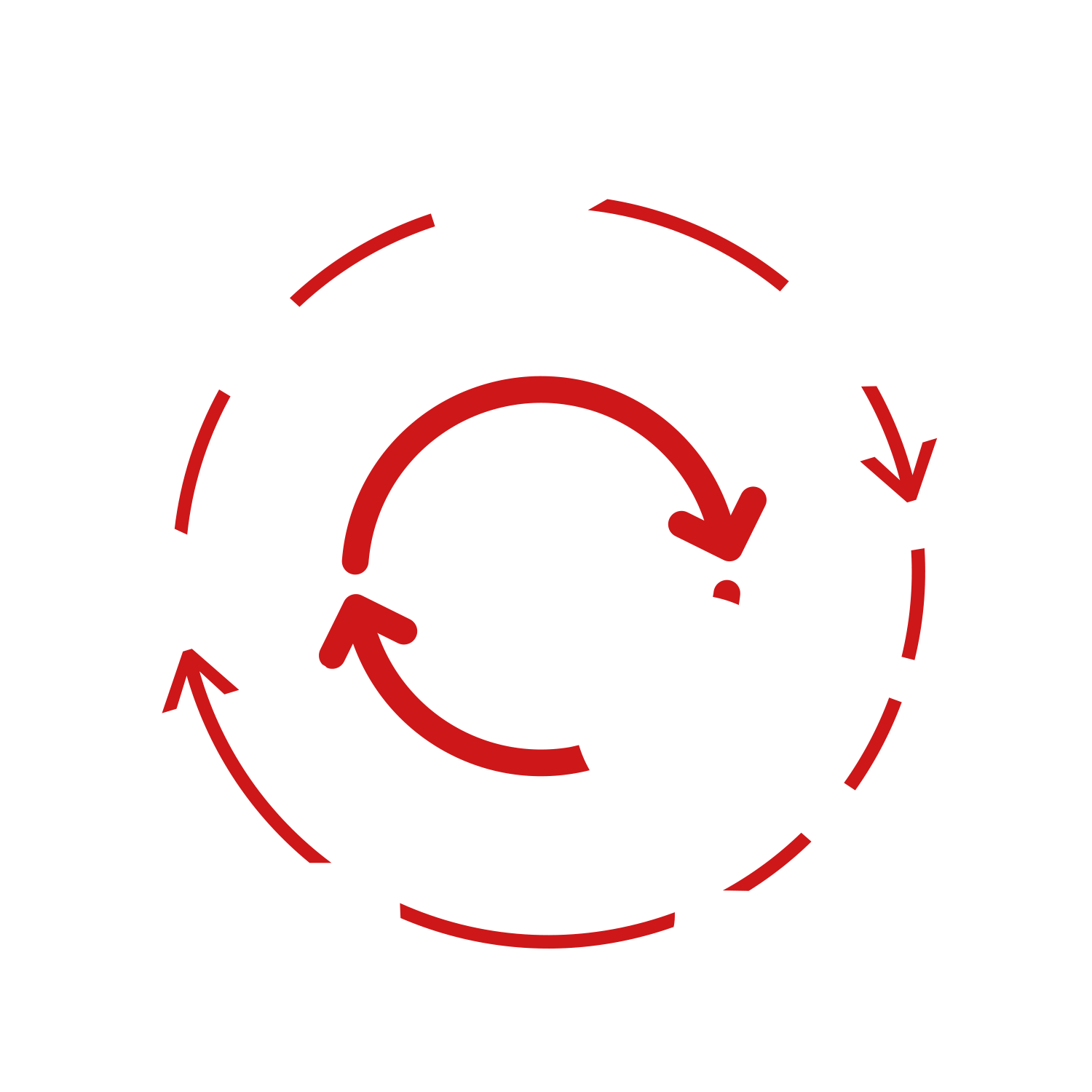