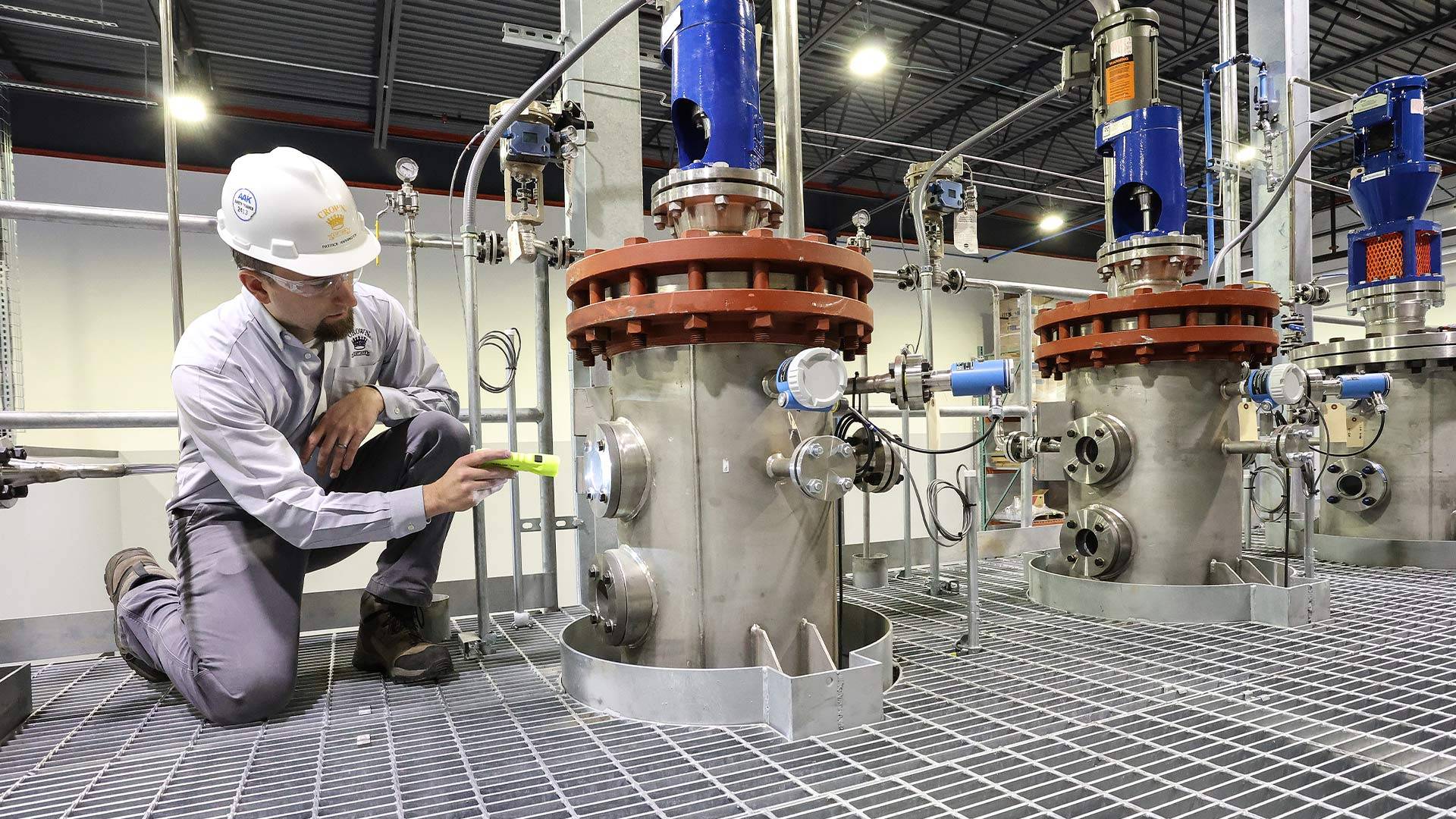
The Crown biodiesel distillation process can be used as a method to clean up a methyl ester that does not meet the proper biodiesel specification. However, it is usually designed to make biodiesel into even better quality biodiesel by improving the cold flow characteristics. This is accomplished by distilling the biodiesel and leaving behind a lot of the monoglycerides and other low-volatile components.
Crown uses a high-vacuum, high-temperature distillation column to separate the desired biodiesel components from the undesired components. The high-quality biodiesel produced can far exceed the quality needed for use as a fuel. Therefore, it is sometimes used for only a portion of the produced biodiesel and then blended with normal biodiesel in order to achieve a nominal gain in quality or to offer a product to customers who desire a product that has a much stricter standard than the normal biodiesel.
Crown Advantages
- Distilled biodiesel can command a premium price in the marketplace because of its performance in cold weather
- Adding equipment for heat economization adds capital cost, but saves a lot of money in operating expenses
- Distillation helps to alleviate an existing biodiesel plant’s shortcomings if the problem is related to the transesterification reaction; a cost analysis should be performed to see if fixing/tweaking the biodiesel plant would make more economic sense
Crown Design Features
- A high-vacuum process assures minimal time spent at high temperatures, lessening the chance for product degradation
- Maximum use of heat economization
- Distillation equipment can be designed for a range of feedstock and product specifications